Do you know how to make a perfect MIG weld?
Many welders learn to weld with tig finger on their own, in a company or take courses at institutions. This is probably your case.
It turns out that only the basics of welding are taught, with some extra finishing techniques. This is not a problem, as it is necessary to work as a welder.
So, in this text, you will see what you should do and what not to forget, so that your MIG weld is as perfect as possible.
Tips on how to make a perfect MIG weld
1 – Clean, Clean and Clean!
The number one flaw when doing MIG welding is porosity. And the general reason of porosity is soldering painted, dirty or oily surfaces.
All of this can “contaminate” the solder, causing holes that look like sponges.
It is necessary to clean, sand, grind the surface, removing dust, paint and other things that can contaminate the solder.
2 – Use the Negative Claw Well
Some experts say this is a common reason of welding errors.
Many welders don’t care if the grapple is in good condition or securely fastened. They keep dropping wire even though the torch is choking.
For better performance, look for the tig welder for sale.
3 – Keep the End of Wire Short
Generally, keep the wire size passing from the contact tip around 0.5cm to 1cm.
According to experts, this single tip will make a big difference in the result of your weld.
4 – Listen Well to the Soldering Sound
You know that story of listening to your “inner self”?
So, only this time it’s the Inner Welder. You need to recognize the sound of soldering when it is well regulated, when the voltage is above or below ideal. For better management of voltages, always use mig welder for sale.
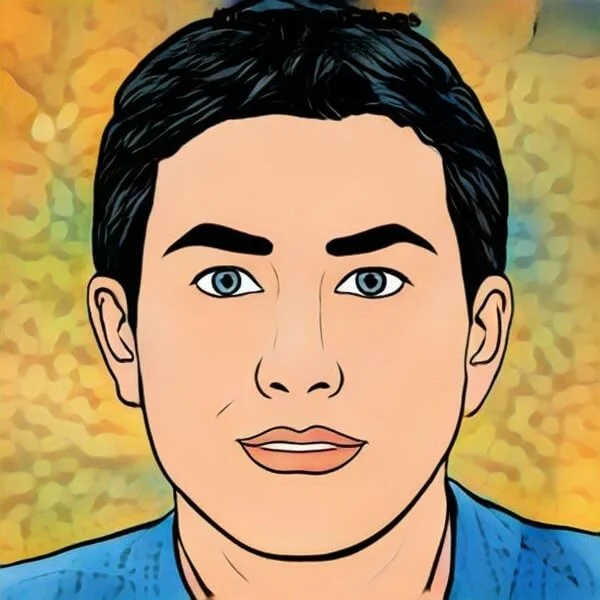
Ryan Myers is a business blog author and writer. He graduated from the University of California, Berkeley in 2009 with a degree in Political Science. His favorite topics to write about are blogging for small businesses and becoming an entrepreneur.